2019年,万翔冷链围绕公司年度工作计划,制定“降低人工成本占比”精益改善项目。截止至2019年8月,公司成功将“人工成本/变动成本”由2018年的65.6% 降低至61.4%,“人力成本/ 总收入” 由2018年的47.8%下降至44.5%,本期的精益改善案例分享项目团队如何开展精益项目工作。 万翔冷链精益改善团队深入现场了解,分析现状原因,利用精益改善可视化管理、5S、微创新和制定标准作业工具等方法,成功找到并解决人工成本高居不下的问题,并制定了一系列精益化的作业环节与改善措施。 实行准时化作业 改善团队通过研究发现,现场作业人员夜班时间过长。夜班作业人员共4人,工作时间从当日20时至次日8时,其中正常工作时长8小时,加班时长4小时。如此下来,夜班作业人员每月共计会产生480个小时的加班时长。 改善团队根据实际作业情况,对夜班上班时间提出改善方案:由现场主管对夜班作业量和时间段进行合理评估,并契合客户的下单时间,来决定夜班人员的上班时间。此举最大程度上保证了人力资源的合理配置,提高夜班作业人员的效率,控制人力成本。 实行分岗作业 改善前, 库内外收发拣货人员在同一组共同进行作业,复核环节缺失。因各库区客户货量和下单时间段的不同,出现1组在客户预约时间内无法捡出所需货物,2组却无货可收(发)的局面。而主管需处理库内外异常,工作量较大,无法及时对人员进行调配,产生人力资源浪费。 经改善团队研究试行后,将原先低效的两个工作组按岗位不同进行重新分组。团队构成分别为库内拣货组和收发组,做到库内分拣、站台收发复核,将异常控制在装车或入库前。不仅有效控制异常发生,还易于对作业人员进行考核。 优化拣货动线 减少无效走动 改善前,各客户存在库内的货物储存位置分散,库内拣货人员行走动线因存储货物分散,导致动线长且乱。 改善后,按照客户集中存储并根据系统运算将出库频率高的产品放置在一层零拣位,优化拣货人员行走动线,减少叉车升降高度,降低叉车升降频率,从而提高单位时间内拣货效率。 提高多纵深货架利用率 改善前,万翔冷链以仓配客户为主,仓配客户产品的货物多以小体积、零散产品为主,原有的多纵深储位适合存放存储型客户产品,仓配客户产品与当前货架类似不匹配,导致多纵深储位空间浪费。 改善后,万翔冷链根据多纵深货架、产品类似、特点自行设计轻型货架。轻型货架标准四层,也可依据产品规格大小,进行调整层高及层数。每个多纵深储位可放置三组移动货架,共计十二层,较原来只能放置6 托货,大大提高了储位利用率,也提高员工拣货效率。 此外,万翔冷链项目团队在改善过程中发现单证作业流程、现场人员配置及现场作业流程等环节还有优化空间,希望通过努力,持续改进,向项目指标再进一步! 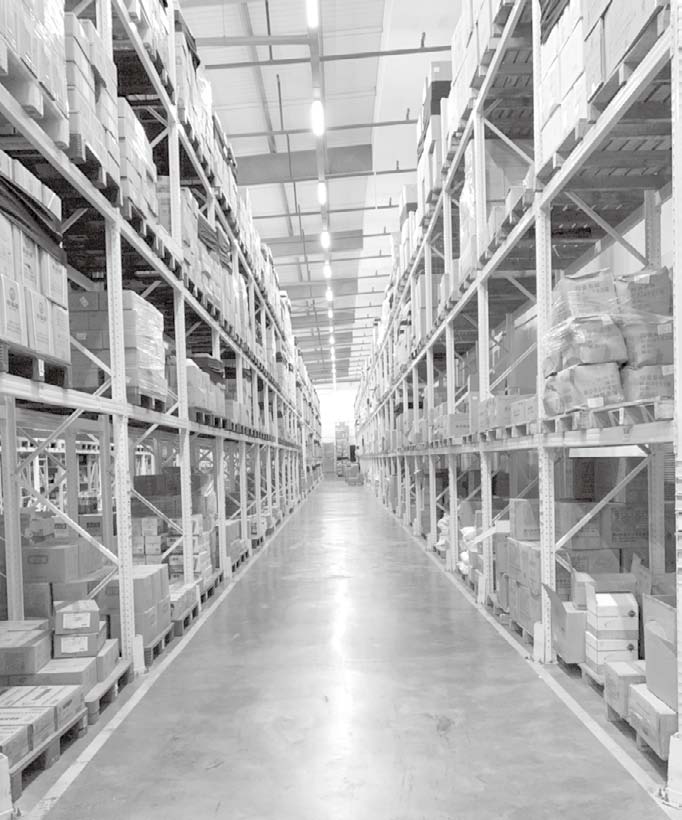 万翔冷链 王紫恒 |