■ 集团运标部 叶礼辉 作为丰田生产方式(精益管理来源于丰田生产方式)创始人的大野耐一曾经在生产车间对工人们说:“我可以请求你们每天至少做一小时创造附加价值的工作吗?”任何没有为客户创造附加价值的活动都称为浪费。 大野耐一是第一位意识到现场存在大量浪费的人。精益管理将生产现场的不增值活动归类为“七大浪费”:搬运的浪费、库存的浪费、动作的浪费、等待的浪费、过度加工的浪费、过量生产的浪费和不良的浪费。1、搬运的浪费。搬运是一种不产生附加价值的动作,这里包括物品移动所需要的时间的耗费,人力、工具的占用。2、库存的浪费。 库存的浪费主要表现在:产生不必要的搬运、堆积、放置、防护、寻找等浪费的动作;占用资金及额外的管理费用;物品的价值衰减;占用空间的浪费。库存的浪费被视为最大的浪费,是“万恶之源”。3、动作的浪费。生产现场作业动作的不合理导致的时间浪费。4、等待的浪费。因断料、作业不平衡、计划不当等造成现场员工无事可做的等待而造成的浪费。5、过度加工的浪费。一是指多余的加工;另一方面是指过分精细的加工,造成资源的浪费。6、过量生产的浪费。生产过度、过早或超出客户的需求。7、不良的浪费。是指生产现场发生不良品,需要进行处置的时间、人力、物力上的浪费。根据调查统计表明:就平均水平来说,在生产车间,占总时间大约10% 的作业(或活动)是为客户创造价值的,比如装配锁螺丝等;而30% 的活动是不增值的,但在现有条件下是不可缺少的,比如产品外观质量检查和填写记录单等;那剩余60% 的活动就属于浪费,比如:走动、搬运和弯腰等。 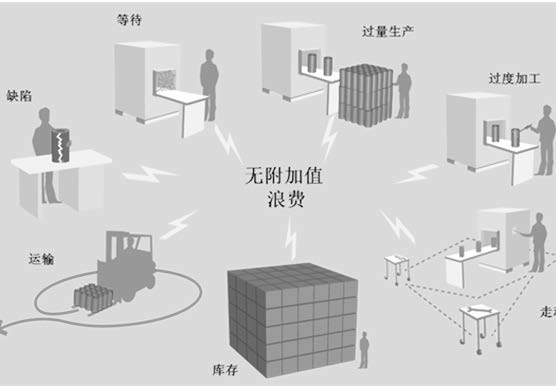 |