■集团运标部 叶礼辉 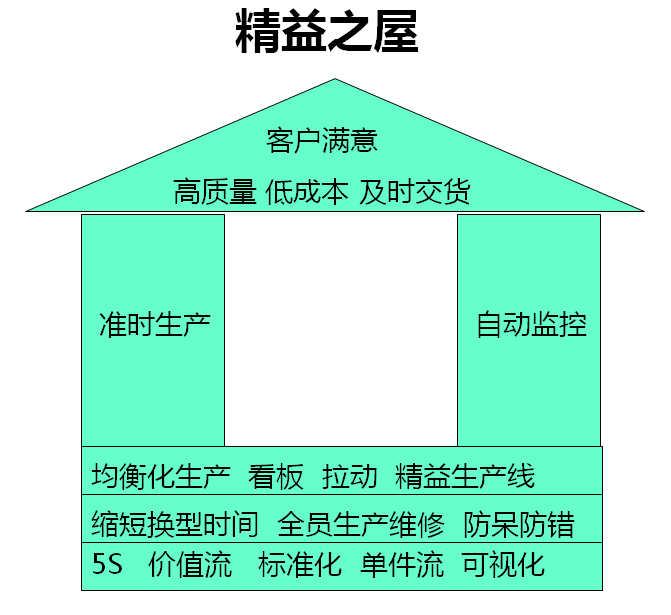 源于日本丰田生产方式(TPS)的精益管理,是继泰勒科学管理法和福特大量装配线方式之后世界生产方式的第三座里程碑,被喻为“改变世界的机器”。精益管理是基于流程彻底地去除各个环节的浪费,以最低成本生产出最高品质产品的管理运营方式。如何通过推行精益管理来降低企业耗费?针对集团的特点,我们重点就精益管理的以下几个方面进行探讨和思考。 消除浪费 专注为客户创造价值 精益管理的核心理念是消除生产现场的一切浪费,只做给客户创造价值的活动。精益管理将生产现场的不增值活动归类为“七大浪费”,包括不良品浪费、过度加工浪费、动作不合理浪费、搬运浪费、库存浪费、过量生产浪费和等待浪费。 准时生产(Just In Time)和自动监控(Jidoka)是精益管理的两大支柱。准时生产指在必要的时间内生产必要数量的必要产品,以杜绝过量生产,消除浪费,降低成本。看板是保证准时生产的工具,这种现场自律微调的“后补充”生产,以多品种、高质量、低成本、零库存为目标,很好地响应了市场需求。自动监控是指赋予机器以人的智慧,出现异常就立即停机,防止了错误的继续传递,这种防止失误装置,能够防止生产不良品,能自动控制现场发生的异常情况,使人从机器旁解放出来。 精益管理通过运用标准化作业等精益工具和方法,以准时生产和自动监控为两大支柱,实现低成本、高质量和及时交货的目标,最终达到客户满意。附图“精益之屋”能够帮忙更好地理解精益管理体系。 精益管理是一个全员参加、不断改进的降低成本的体系过程。精益管理的推广要从局部试点开始,但不能限于局部、孤立存在,更不是表面工具的模仿。 精益改善 持续引入运行标准化 精益改善活动是精益管理体系中最重要的内容之一,3至8人的小团队在为期3周的时间内对生产现场或流程进行改进,通过去除生产现场或流程等环节中的不增值活动(浪费),达到降低成本,提高质量或者缩短周期的目的,从而提高企业效益。 在倡导精益改善活动的同时,如何正确对待运行标准化管理?如果单纯把改善当成对标准的否定,不把标准化引入到改善活动中,实际上是对改善活动的一种误解。保持现有技术、管理和作业上标准的活动,和改进现有标准都是完全必要的,这是任何管理体系努力追求的持续改善的目标;在涉及标准的改善活动在经过PDCA循环后,必须建立现场标准化流程,保证标准的改进和维持,二者就不会有任何冲突。实际上,改善活动在发现变异、缺陷时的第一个问题应当问“是否因为没有标准?是否没有遵守标准?是否需要改进标准?是否需要建立新的标准?” 循序渐进 四阶段推行精益管理 精益管理已经在许多优秀的中国企业中得到应用,帮助企业在降低成本、提升质量和提高对市场的快速反应。企业如何推行精益管理?笔者认为要分成四个阶段进行:第一阶段是精益理念培训和项目前期现场调研;第二阶段着重于生产现场的管理优化和生产系统的改善,生产现场的管理优化包括现场5S,可视化和标准作业等基础性的工作,而生产系统的改善则是指价值流分析,单件流,看板拉动,U型生产线和自动监控等;第三阶段是精益供应链,从产品研发开始到原材料采购、物流运输、生产制造、交货给客户到最后收到货款,在整个供应链中如何消除对客户不增值的活动,缩短周期时间,提高客户满意度。第四阶段是精益文化和精益组织的形成。 佰翔洗涤正在推行精益改善项目“布草车间生产效率改进项目”,改善团队在布草洗涤现场通过消除不增值的活动(浪费),重新布局巾类折叠区,优化洗涤龙装仓工位和大烫机整理/送进工位的标准作业,以提升巾类折叠区人工效率和大烫机的设备效率。 作为运行标准化工作的一部分,精益管理主要在集团的生产型和物流型企业推行。2014年以佰翔洗涤为试点,将通过持续的精益改善项目来降低洗涤公司的人工成本和能耗,提高企业效益;2015年将在更多的成员企业如佰翔空厨、万翔现代、万翔冷链等公司导入精益管理。 |